inTEST EMS Innovations
Extreme Environmental Testing
With the rapid proliferation of semiconductors in industrial and automotive applications, more stringent testing is required to ensure semiconductor ICs will operate reliably in the extreme environments in which they must function. These conditions range from the very cold (-55°C) to the extremely hot (+200°C) temperatures. inTEST EMS has products that are specifically designed and manufactured to maintain tolerances and specifications through larger temperature ranges.
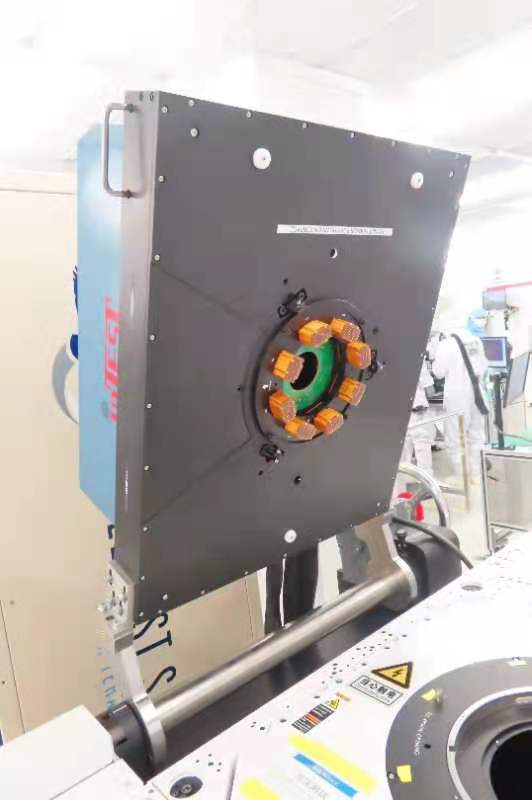
Ultra High-Power
The sweeping adoption of Electric Vehicles, Renewable power, and other High-Power opportunities has transformed the specialized IGBT and Power IC business. Requirements for high volume testing have forced the industry to adopt new high parallel, cost-effective, and optimized test platforms in order to meet the performance, time to market, and financial requirements of today’s high-power devices.
inTEST EMS now offers new solutions for high-power interface docking platforms with its side-mounted hinge assembly that minimizes the overall test cell footprint and eliminates the need to remove the test head assembly from the probe for proper maintenance.
Test up to 16 devices at a time. With 50 probes per module and each probe individually rated for 5 Amps DC, the probe pin ring has been successfully used at 3KV/300AMP. The interface can be configured to meet your device requirements and test throughput with different pogo modules.
Automation
Introducing the first automated manipulator available in the ATE industry. Docking the first time, every time—that’s smart manufacturing. Following initial teaching of various peripheral docking and service positions, “One Touch” docking can be repeatedly executed with the use of a remote pendant.
Helping you drive to your ultimate goal: maximizing OEE (Overall Equipment Efficiency)
Improve Quality

Increase Productivity




Enhance safety


Reduce Downtime

